
Wafer: the heart of modern technology
Wafer, as the basic material of semiconductor devices, has been an indispensable part of modern electronic equipment since its birth. With the development of science and technology, wafers are more and more widely used in smart phones, computer chips, automotive electronics and other fields, and become an important force to promote scientific and technological progress. The history of wafers can be traced back to the 1950 s, when the invention of the silicon transistor marked the beginning of the semiconductor era. Nowadays, wafers have developed into a highly precise material, and its parameters such as purity, thickness and diameter directly affect the performance and reliability of electronic devices.
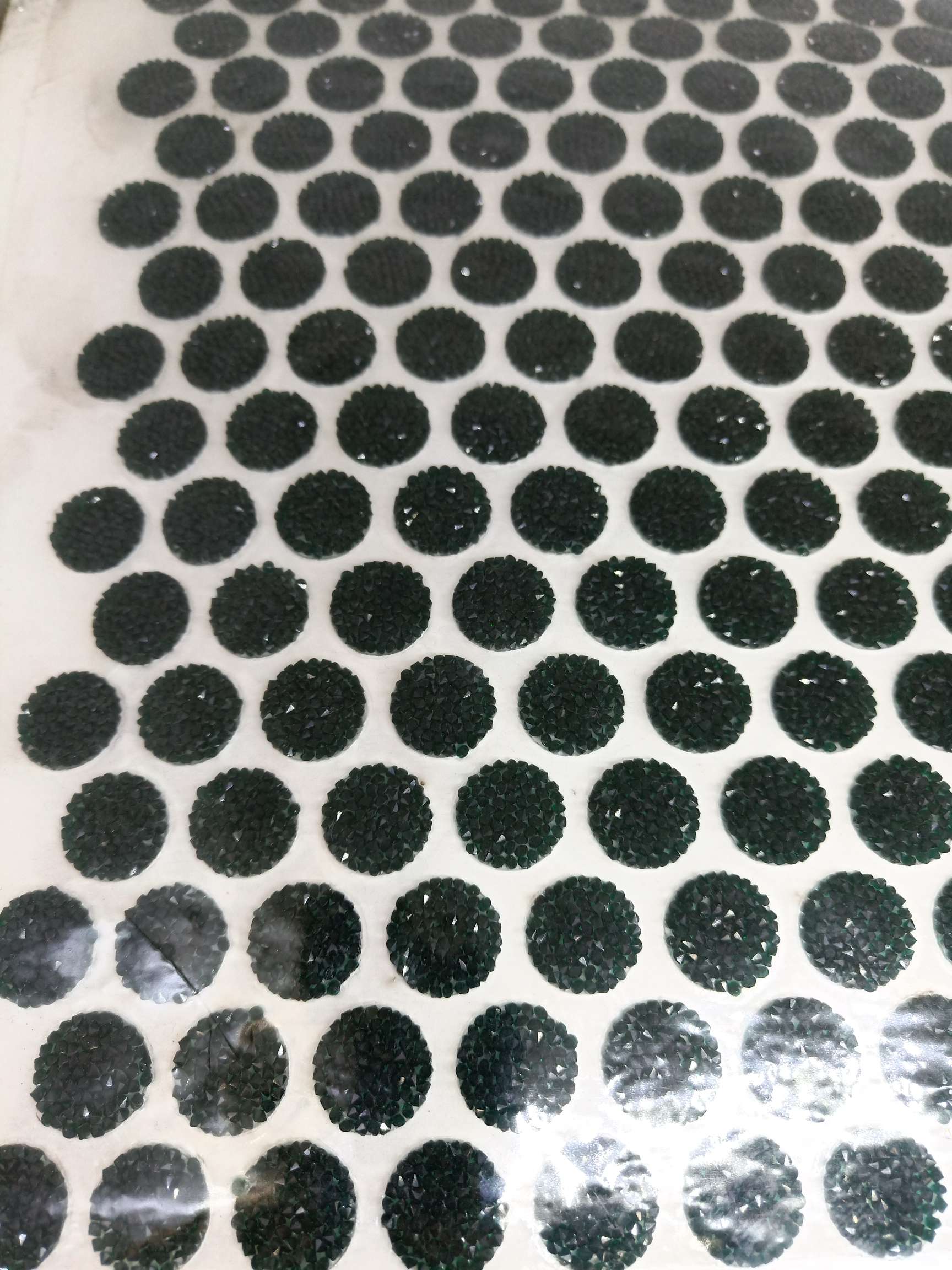
Technical characteristics of wafers
Key technical specifications for wafers include purity, thickness, and diameter. The higher the purity, the less impurities inside the wafer, thereby reducing interference during signal transmission and improving the performance of electronic equipment. The thickness determines the mechanical strength and thermal conductivity of the wafer, and too thick or too thin will affect its use effect. Diameter is an important parameter to measure the wafer size. At present, the mainstream wafer diameters on the market are 200mm and 300mm. Choosing the right wafer for your needs requires a combination of these parameters and their impact on performance.
Wafer production process
The production of wafers is a complex and delicate process involving multiple steps. The first is the choice of raw materials, commonly used materials are silicon, gallium arsenide and so on. This is followed by smelting and drawing monocrystalline silicon rods, a process that requires extremely high temperature control and a clean environment. Subsequently, the single crystal silicon rod is cut into thin slices, and then through grinding, polishing, cleaning and other processes, finally forming a qualified wafer. In the entire production process, every step requires strict quality inspection to ensure the quality and performance of the final product.
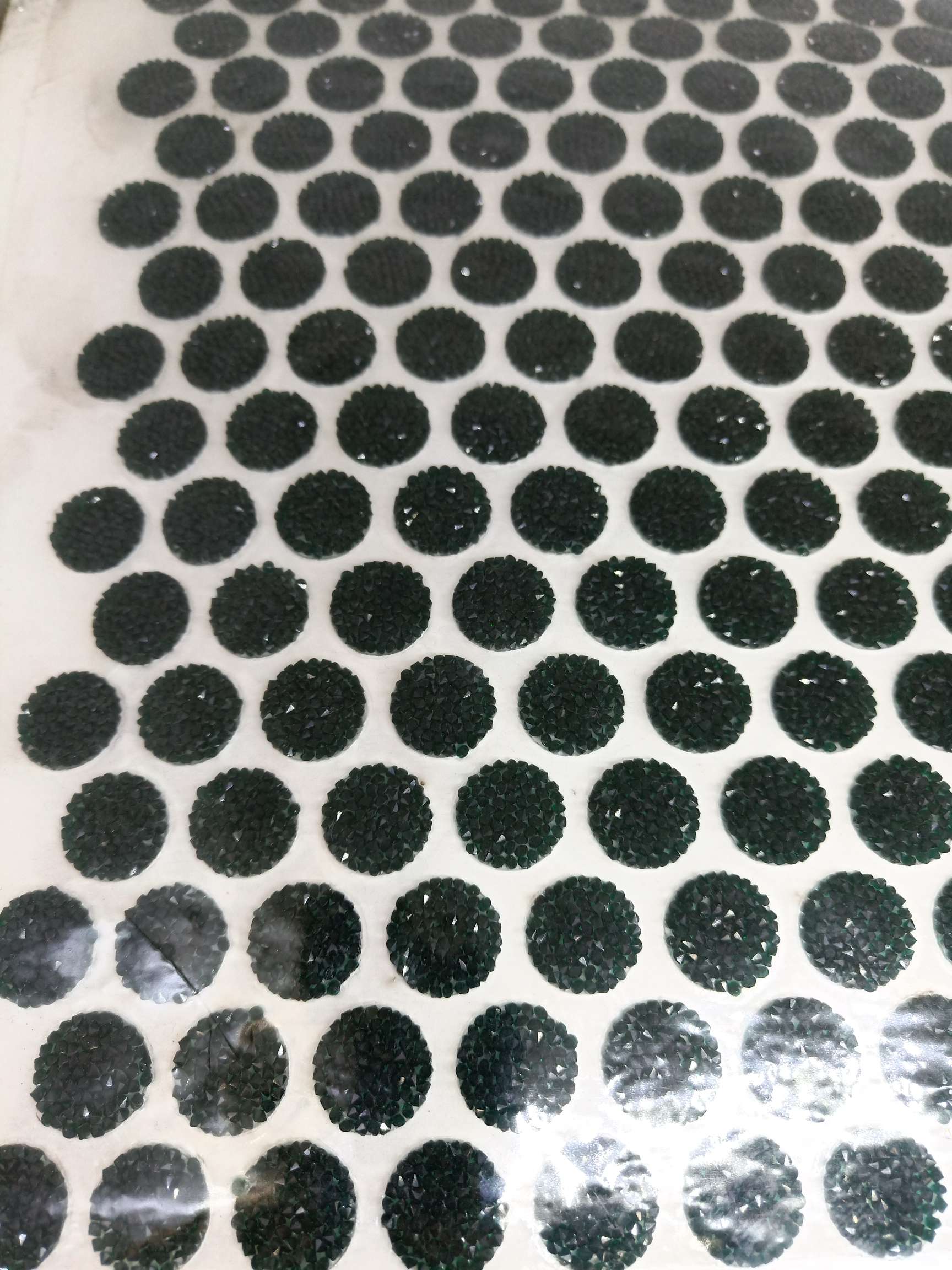
Wafer Applications
Wafers are widely used in modern electronic equipment. For example, in smartphones, wafers are used to make CPU, memory and other key components, greatly improving the computing power and life of the phone. In computer chips, wafers are even more indispensable. Whether it is desktop computers or servers, high-performance processors are based on wafer manufacturing. In addition, automotive electronic systems also use a large number of wafers, from navigation systems to autonomous driving technology, wafers play an important role in them.
Future Trends in the Semiconductor Industry
At present, the semiconductor industry is in a stage of rapid development, and market dynamics and technology trends are changing with each passing day. The rise of emerging technologies such as 5G communication, artificial intelligence (AI) and Internet of Things (IoT) has put forward higher requirements for the wafer industry. In the future, wafers with higher integration, lower power consumption and stronger computing power will become the mainstream of the market. At the same time, with the enhancement of environmental awareness, green production and sustainable development will also become the focus of attention of enterprises.
Choose the right wafer supplier
Choosing a high-quality wafer supplier is the key to ensuring product quality. First, examine the supplier's technical strength, including its R & D investment, the number of patents and the size of the technical team. Second, evaluate the supplier's production capacity to see if its production line is advanced and its production capacity is sufficient. Finally, understand the supplier's customer support and service system, including after-sales service and technical support. Well-known brands such as TSMC and Intel are trustworthy choices.
Quality and Testing of Wafers
The quality inspection of the wafer is an important work, mainly including the inspection of surface flatness, impurity content, resistivity and so on. Common defect types are cracks, scratches, contamination, etc., which may cause wafer failure or performance degradation. In order to ensure the quality, can use optical microscope, scanning electron microscope and other tools for detection. In addition, automated testing equipment can be used to improve testing efficiency and accuracy.
Wafer Cost and Benefit Analysis
The cost structure of wafers is complex, including raw material costs, depreciation of production equipment, and labor costs. In order to reduce costs on the premise of ensuring quality, we can start from the following aspects: first, optimize the production process and improve the yield; second, strengthen supply chain management and reduce the cost of raw material procurement; third, introduce advanced production equipment to improve production efficiency. Through these measures, not only can reduce the overall cost, but also enhance the competitiveness of products. Case studies show that cost-effective wafers can not only bring significant economic benefits, but also win more market share.
Environmental Protection and Sustainable Development
The wafer production process will produce a certain amount of environmental pollution. Therefore, environmental protection measures and sustainable development strategies are particularly important. Many leading wafer manufacturers have already started to take actions, such as using clean energy, reducing wastewater emissions, and recycling waste materials. At the same time, companies are also actively applying for international environmental certification such as ISO 14001 to demonstrate their efforts in environmental protection. When consumers choose wafer products, they can also give priority to those companies that pay attention to environmental protection and jointly promote the green development of the industry.
Interactive Q & A: Answer your questions
To better serve our readers, we have created an interactive session to answer some of your frequently asked questions about wafers. The following are a few typical Q & A, I hope to help you:
- Q: How to judge the quality of the wafer? Answer: The quality of the wafer can be judged by indicators such as surface flatness, impurity content, and resistivity. In addition, a more comprehensive assessment can be carried out with the help of professional testing equipment.
- Q: What are the common defect types of wafers? A: Common defect types include cracks, scratches, and contamination. These defects may cause wafer failure or performance degradation, so special attention is required.
- Q: How to choose the right wafer size? Answer: When choosing a wafer size, you need to consider the application scenario and performance requirements of the final product. Generally speaking, larger wafers are suitable for high-end products, while smaller wafers are more suitable for low-cost, high-volume production occasions.