
Basic concepts of wafer
Wafer is a basic material used to manufacture integrated circuits, usually made of high-purity silicon or other semiconductor materials. Understanding the basic characteristics and classification of wafers will help us to better understand their important position in the high-tech industry. The diameter of the wafer can vary from less than 1 inch to 12 inches, and different sizes are suitable for different application scenarios. The surface of the wafer must be extremely flat and smooth to ensure a high degree of consistency and reliability of the chips fabricated on it.
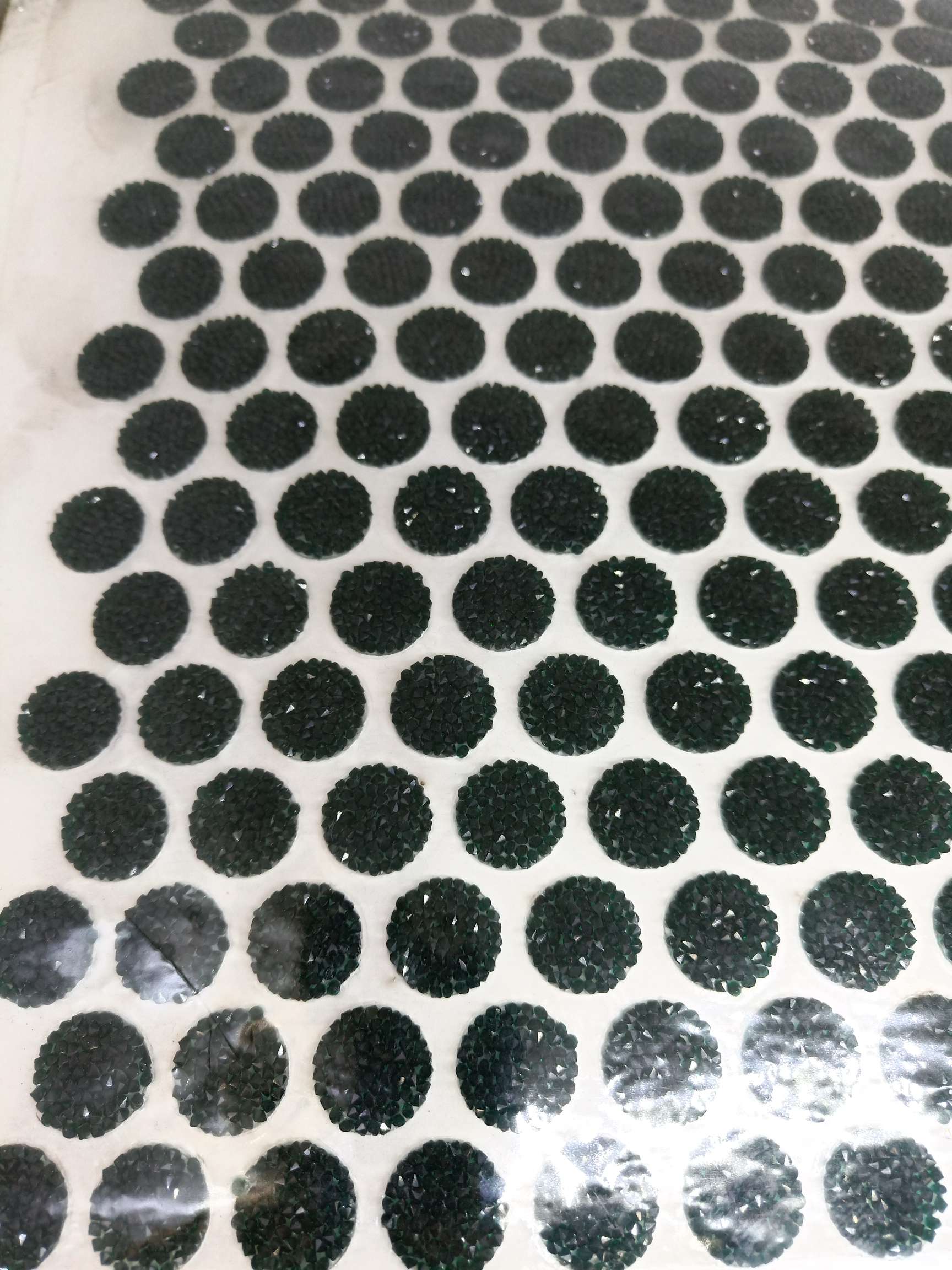
Wafer production process
From the preparation of raw materials to the delivery of finished products, the wafer production process involves multiple complex steps. First, it is necessary to extract single crystal silicon from a high-purity silicon material, a step called single crystal growth. Next, the single crystal silicon is cut into thin slices, a process called slicing. Subsequently, grinding and polishing are performed to achieve an extremely high flatness of the wafer surface. Finally, through cleaning and inspection, to ensure that the quality of the wafer meets high standards. Each step requires precise processing and strict control to produce high-quality wafers.
Wafer performance characteristics
The reason why wafers have become the core material for high-performance chip manufacturing is closely related to their unique physical and chemical properties. The wafer is extremely pure and almost free of impurities, which makes the chips manufactured on it have higher stability and reliability. The uniformity of the wafer is also very important, which means that the properties and thickness of the material are very consistent across the entire wafer surface. In addition, the surface flatness of the wafer is also an important indicator of its quality, and the smooth surface is conducive to the subsequent chip processing process.
Wafer Applications in the Semiconductor Industry
Wafers are widely used in the manufacture of various semiconductor devices, such as microprocessors, memories, sensors, etc. For example, in smartphones, wafers are used to fabricate core processors and memory chips, enabling efficient computing and data processing capabilities. In the field of automotive electronics, wafers are used to manufacture various sensors and controllers, improving the safety and comfort of vehicles. Through specific case studies, we can see the practical application of wafers in different fields and their role in promoting the development of modern science and technology.
Technical Challenges and Prospects for Wafers
With the continuous development of science and technology, wafer manufacturing is facing many new technical challenges, such as size reduction and power consumption reduction. For example, in order to improve the integration and performance of the chip, the size of the wafer needs to be smaller and smaller, which puts forward higher requirements on the manufacturing process. At the same time, with the increasing demand for energy efficiency, how to reduce low power consumption on the premise of ensuring performance has become an important research direction. In the face of these challenges, researchers are constantly innovating and developing new technologies and materials to promote the further development of wafer technology.
Choose the right wafer supplier
There are many wafer suppliers in the market, how to choose a reliable partner? First of all, we should consider the technical strength and production capacity of suppliers, and choose those enterprises with advanced production equipment and mature technology. Secondly, we should pay attention to the quality management system of suppliers to ensure that the wafers produced by them meet international standards. Finally, a supplier's reputation and service level can be assessed by looking at customer reviews and success stories. Taking these factors into account can help companies make informed decisions when purchasing.
Wafer quality inspection and certification
Ensuring the quality of the wafer is a prerequisite for manufacturing high-performance chips. Common quality inspection methods include optical inspection, electrical testing and mechanical testing, which can evaluate the performance indicators of wafers from multiple angles. In addition, there are many authoritative certification bodies in the world, such as ISO 9001 and SEMI, which have formulated a series of strict standards and specifications to help enterprises ensure the quality of wafers. Through these tests and certifications, the reliability and market competitiveness of wafers can be greatly improved.
Future Trends of Wafers
With the rise of emerging technologies such as artificial intelligence and the Internet of Things, the demand for wafers will continue to grow. Especially in the fields of smart wearable devices, smart home and automatic driving, the demand for high-performance chips is increasing. This will drive the continuous innovation and development of wafer technology, for example, the development of larger size and higher purity wafers to meet the needs of the future market. At the same time, the application of new materials and new processes will also bring more possibilities for wafer technology.
Environmental Measures for Wafer Manufacturing
Environmental protection is an important issue in modern manufacturing. In the wafer manufacturing process, companies have taken many environmental protection measures, such as recycling water resources, reducing the use and discharge of chemicals. These measures not only help protect the environment, but also reduce the operating costs of enterprises. By implementing the concept of green manufacturing, enterprises can achieve sustainable development while ensuring product quality.
User feedback and success stories
By sharing users' actual feedback and success stories, we can better demonstrate the performance and advantages of wafers in practical applications. For example, a well-known mobile phone manufacturer has significantly improved the performance of its new mobile phone after adopting high-quality wafers, which has been widely praised by consumers. Another example is a car manufacturer that has significantly improved the safety of its vehicles by using advanced wafer-made sensors. These real cases can not only increase the trust of readers, but also provide valuable experience for other enterprises.