
Wafer: the core cornerstone of semiconductor chips
Back in history, the story of the wafer began in the laboratory. Initially, scientists explored new possibilities in the microscopic world in order to achieve the goal of higher integration and smaller size. With the passage of time, this technology has gradually matured and entered the stage of large-scale industrial production. In this process, many key technologies such as crystal growth methods, doping process and other aspects of innovation continue to emerge, greatly promoting the rapid development of the semiconductor industry.
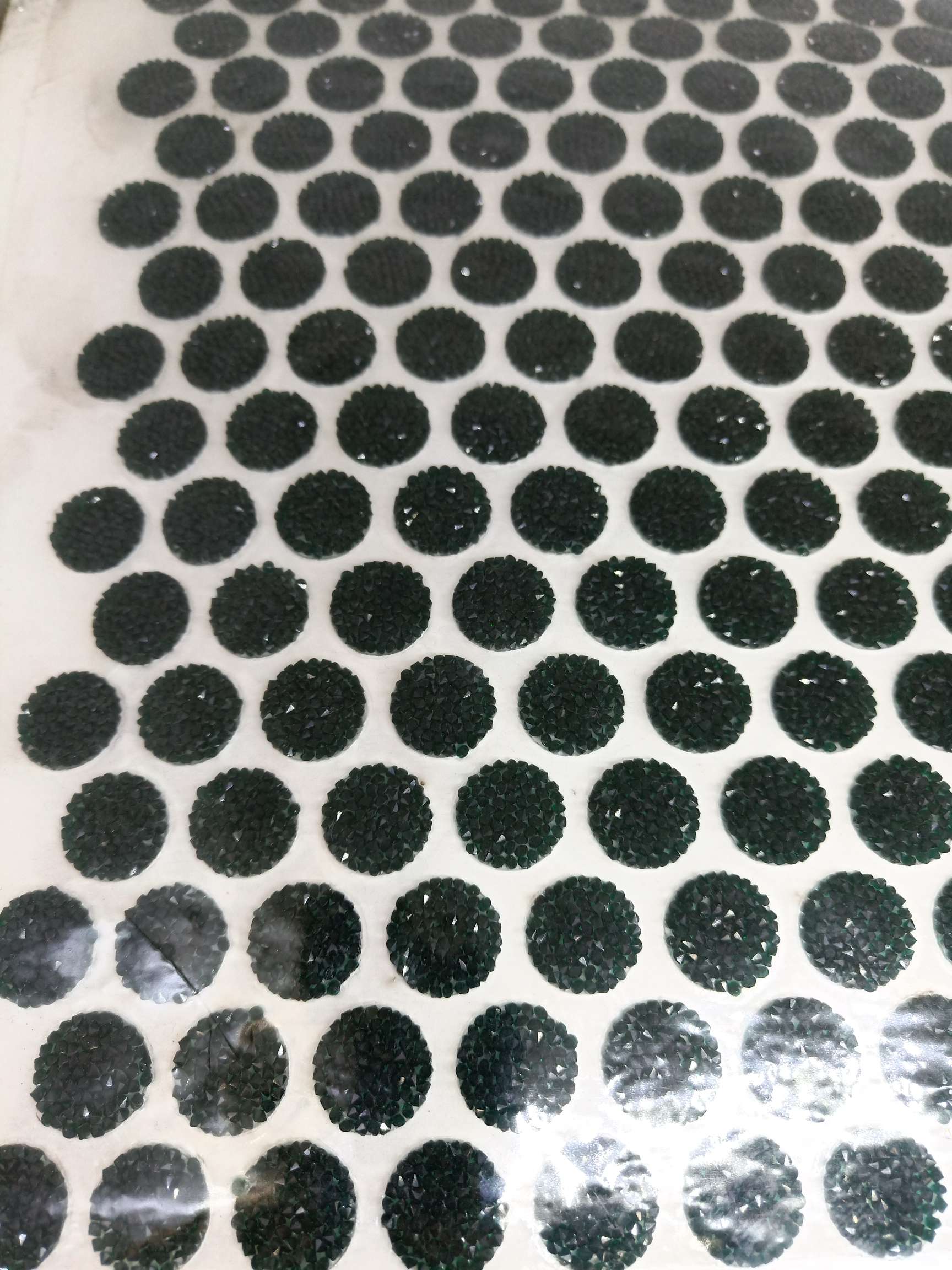
Early scientists developed wafers in the lab
Today, the smart phones, laptops and other smart devices in our hands can have such powerful functions, to a large extent, thanks to the rapid development of wafer technology. It not only changed people's way of life, but also promoted the key force of the whole information technology revolution.
Into the modern wafer production workshop, you will find here is full of mysterious and efficient atmosphere. From the beginning of silicon wafer cutting, every process is a process of excellence. First, the silicon ingot is accurately cut into silicon wafers as thin as cicada wings through advanced mechanical arms. Then there is chemical vapor deposition (CVD), where gas molecules will decompose in a high temperature environment and form a uniform and dense film on the silicon surface. Then there is the lithography technology, which uses ultraviolet rays to irradiate photosensitive adhesive film to draw circuit patterns. Finally, there is an etching step to remove materials in unilluminated areas, so as to accurately depict the required nano-scale lines.

Scenarios of high-precision equipment operation in modern wafer production plants
Not only that, today's production lines also introduce a lot of automation equipment and strict quality control systems. The robot arm can perform repetitive actions in milliseconds to ensure consistency and efficiency, while the real-time monitoring system can capture any slight deviation at any time and adjust the parameters in time to ensure the high quality level of the final product.
When talking about why silicon has become the most commonly used wafer substrate material, we have to mention its many advantages. First of all, silicon, as a naturally occurring element, has good electrical conductivity and is easy to process into various forms of morphology. Secondly, it has excellent thermal stability and can maintain stable electrical performance under extreme conditions. In addition, silicon dominates the market due to its relatively low cost and better supply chain than other potential alternatives such as gallium arsenide or silicon carbide.

Schematic diagrams of different types of crystal structures observed under the microscope
Although many new materials have emerged in recent years, at present, based on cost-effectiveness considerations, it is difficult to shake the status of silicon in the short term. There may be more breakthroughs in the future, but in the current and foreseeable time frame, silicon is still the undisputed best choice.
In the past few decades, wafer diameters have undergone significant changes from small to large. Early wafers were only a few inches in size, and now the mainstream standard has reached 12 inches or more. This growth is not an accidental phenomenon, but is driven by both market demand and technological progress. Larger area means that more chips can be accommodated per unit area, thereby reducing the cost of a single device; it also allows manufacturers to produce higher yields in the same time period.

Wafer samples of different sizes at different times
However, with increasing size comes new challenges. For example, how to solve the problems caused by stress concentration, improve the yield and other problems need to continue to invest a lot of scientific research resources to overcome. But fortunately, the world's major manufacturers are actively dealing with these problems, and achieved varying degrees of success. Looking ahead, it is expected that the new generation of ultra-large wafers will continue to lead the industry.
Advances in wafer technology have directly driven changes in the downstream electronics market. High-performance processors, memory chips and other new components are emerging, providing consumers with unprecedented speed and low power consumption. Take smart phones as an example. Thanks to the support of advanced manufacturing processes, the current mobile platform can not only run complex applications without pressure, but also greatly improve its endurance. The same applies to the field of notebook computers-thin and portable design concept can be realized, office entertainment is not wrong.

Latest Phones and Tablets with Advanced Process Wafers
In short, it is these invisible but essential underlying technical support that makes our lives more convenient and beautiful. No matter in work or leisure time, we cannot do without those excellent hardware products created by relying on cutting-edge scientific and technological achievements
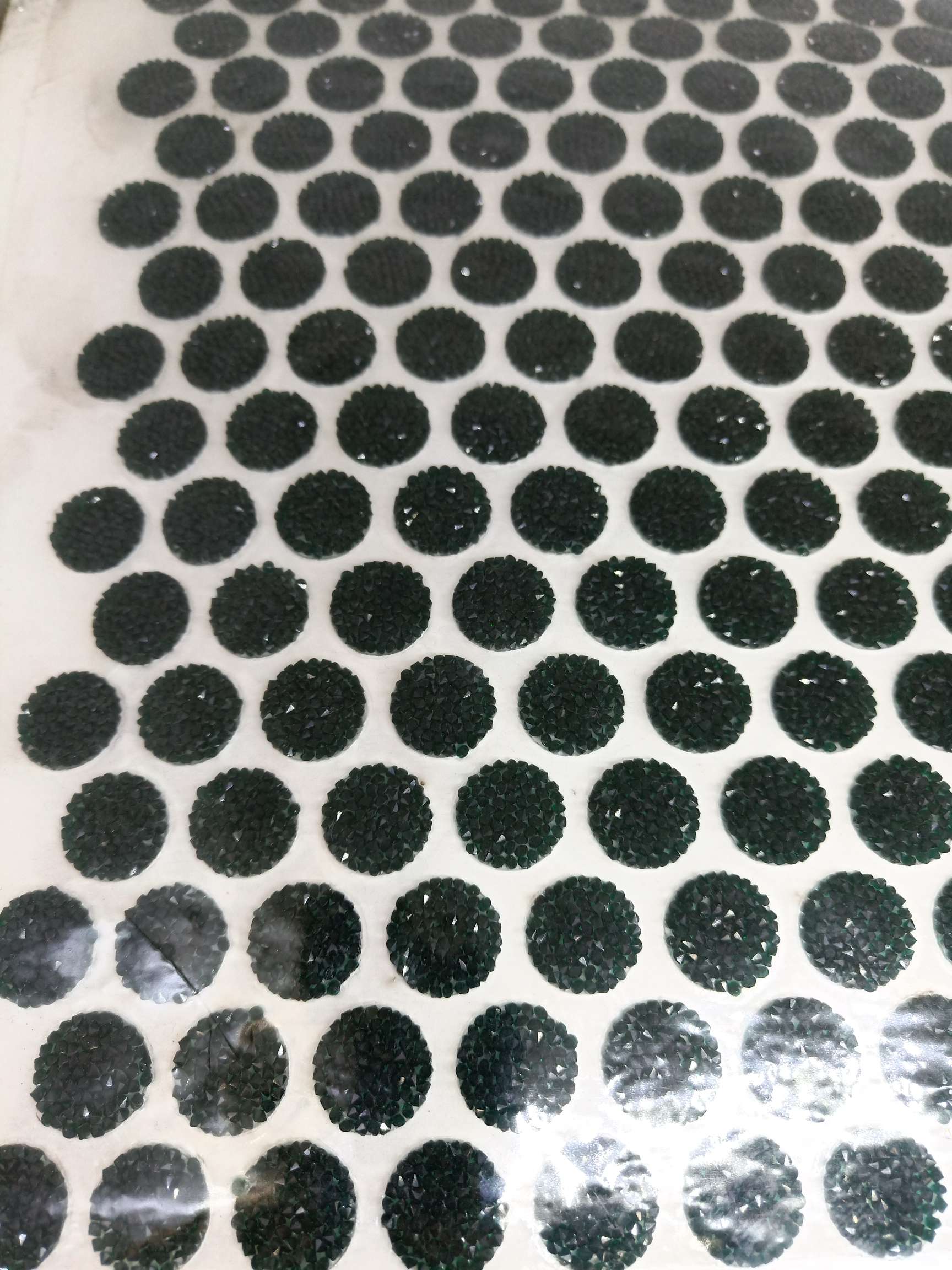